取組事例
多品種小ロット精密部品製造プロセスにおける5G活用型遠隔操作・検品システム開発
ローカル5Gの社会実装に向けて、令和3年に構築した工場向け5Gインフラを活用し(関連記事)、切削機械の遠隔支援の実証、高精細カメラ画像AI分析による3DCADと連携したAI検品システムの開発が行われている。
コンソーシアム:ツウテック株式会社、株式会社ユタカ、株式会社愛媛CATV、システムエルエスアイ株式会社、愛媛県(産業創出課、産業技術研究所)、愛媛大学、徳島大学
中小企業が結束!地域共有型ローカル5Gを用いた遠隔操作支援
金属加工業界が抱える課題
今回の実装実験は、松山市内にある株式会社ユタカ(以下:ユタカ)と東温市にあるツウテック株式会社(以下:ツウテック)の2社間で実施された。
2社は、金属の精密加工を行う、いわばライバル同士の関係だが金属加工業界特有の同じ課題を抱えている。例えば、「シリコンサイクル」という半導体業界特有の需要変動だ。需要があるときは、どんなに設備や人を導入しても仕事が溢れかえってしまう状況になるが、ひとたび需要が減れば、ピタリと機械が止まってしまうほど仕事の発注がなくなってしまう。中小企業にとっては、需要の変動に合わせて人や設備の生産能力を合わせることが困難なのだ。
現在実施されている課題解決策
5Gを使って課題解決!実証実験の内容
これらの課題を解決するために、ユタカが持つデータをツウテックの機械に送り、実際に機械を動かしデータ通りの加工ができるかを確かめる実証実験が行われた。
機械の段取りは、ツウテックのスタッフが装着したスマートグラスから映し出される画像を見ながら、ユタカのスタッフが指示をする。
段取りが完了すれば、ユタカのデータをツウテックの機械に送信するという流れで実施された。
実証実験の結果
精密機械の膨大なデータも5Gを使うことで、短時間での送信が完了。その際、ツウテック側のサーバーにデータが取り込まれることもないため、ノウハウを伝えることなく機械を使用することができた。
実証実験自体は42分程度の短い加工だったが、滞りなく作業は遂行。完成したテストパーツをツウテック側の検査機器で確認後、規格通り正確に加工ができていた。
あらかじめユタカ側で加工していたパーツと比べても、遠隔でツウテック側の機械で加工したパーツは問題なく完成していた。
膨大なデータを短時間で送ることができ、スマートグラスを利用し高精細の画像を確認しながら作業をする今回の実証実験は、高速大容量の5Gだからこそ実現できたといえる。
ライバル会社同士がタッグを組むことでチャンスを逃さない仕組みを作る
今回の実証実験では、遠隔で他社の機械を使った加工ができ、さらに自社のノウハウを守ることもできると確認された。もちろん、他社に出向く時間や手間を省くことも可能に。
「場所も機械も異なりますが、データを相手側の機械に送ることで、指示通りのパーツを製作することができました。これからの社会に大切なのは協調性です。互いが状況によって生産性を補い合う体制を構築できれば、仕事のチャンスを失うことなくクライアントのオーダーに応えることができます。ライバル会社ではなく、協力会社としてwin-winの関係が築けます」とユタカの重森課長は話す。
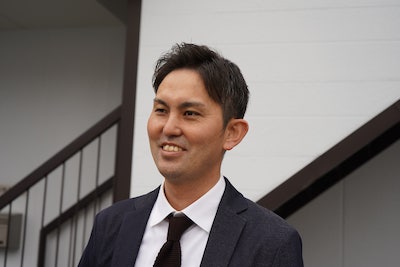
株式会社ユタカ 重森課長
さらに、「今回の実証実験のように地域の同業者が協力し、設備を共有することで設備投資を行わなくても増産につながるようなローカル5Gを活用した地域ネットワークを構築していく予定です」と愛媛県産業技術研究所大塚副部長。
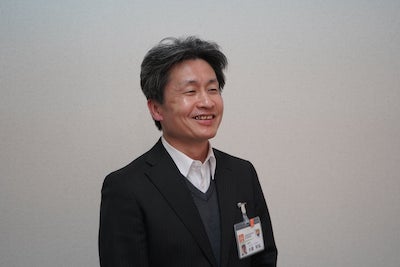
愛媛県産業技術研究所大塚副部長
このように設備共有を行う地域ネットワークの仕組みが整い、県内企業が協力することができれば、大企業並みの受注を受けることも夢ではない!
松山から愛媛、愛媛から四国、そして全国へ。
5Gを利用することで、豊かな社会が実現していくだろう。
多品種小ロットに対応した検品の実現
中小企業が必要としている検品技術とは
令和3年の「課題解決型ローカル5G等の実現に向けた開発実証」を行った際、実証実験自体は有意義なものであったものの、金属加工業の中小企業が実際に利用する場面を考えた際、やり残した課題があった。それが、「多品種小ロットの検品システム」だ。
前回の実証実験で行った検品のシステムは、同一製品の大量生産であればマッチしたシステムだったが、中小企業が主とする多品種小ロットの現場では使いにくい点もあった。今回は、多品種小ロットの検品にマッチした研究開発を行っていく。
現在、開発中!実装は3年後
多品種小ロットの検品システムの開発を担当するのは、さまざまなタイプの検品装置を製造しているシステムエルエスアイ株式会社(以下:システムエルエスアイ)だ。
今の段階で、「多品種小ロットの検品」には、技術的な課題も多い。
これまでシステムエルエスアイが製造してきた装置は、大量生産された物の検品装置が中心だった。今回の多品種小ロットの検品となると、検品対象物の形状に合わせてカメラを移動させていかなくてはならない。この対象物に沿って撮影していく技術を現在構築している。
今年度は各パーツを構築し、来年度にそれぞれのパーツを組み上げ一つの装置にしていく。そして再来年度に実装、という3年計画で進められている。
クリエイティブに働く喜びを
「検品作業は機械に任せて、人々はもっとクリエイティブに働くべき」とシステムエルエスアイの中浦社長。
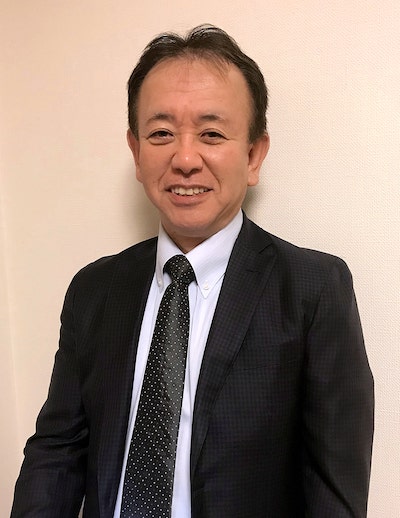
システムエルエスアイ株式会社 中浦社長
多品種小ロット生産に向けた検品機械の開発は、技術的に困難な道のりではあるが、この困難に立ち向かうことで中小企業の課題を解決し競争力アップに繋がる。
世の中にまだ存在しない多品種小ロットの検品装置が完成すれば、多くの人の検品作業の負担を減らすことができるだろう。そういった未来もそう遠くないはずだ。
本取り組み内容が、以下のリンクで紹介されました。
https://www3.nhk.or.jp/news/contents/ohabiz/articles/2023_0210.html
https://www.nhk.or.jp/matsuyama/insight/article/20230113-1.html
本取り組みは、国立研究開発法人新エネルギー・産業技術総合開発機構(NEDO)の5G等の活用による製造業のダイナミック・ケイパビリティ強化に向けた研究開発事業(2022年度)により実施しました。